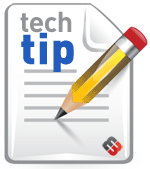
Trying a new epoxy is exciting and challenging, and we would like to share a few thoughts on this subject. Often, there is a tendency to “get right to it” and start the bonding process as soon as possible. In many cases, this may not be a good way to move forward. Epoxies can be tenacious and difficult to remove if something goes wrong.
When the end user receives the epoxy (be it a one component, two component, or UV cure), the epoxy should be cured by itself first, and then on some mock-up parts/substrates. By curing the epoxy by itself, the end user can see exactly how the epoxy cures and check if the hardness matches up (generically) to what is mentioned on the technical data sheet.
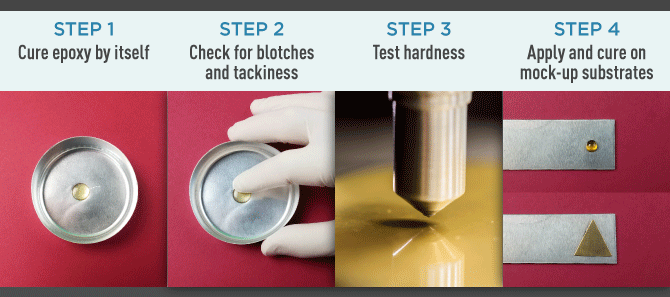
One part systems (either heat activated or UV cured) are much easier to test, and ultimately use. With a two component system, one should mix up a few grams of the epoxy, apply it as a casting or coating, and cure it preferably in an oven (for accelerated cure). This will allow the end user to determine the hardness of the epoxy. If the mix ratio used was incorrect or if parts A & B were not mixed thoroughly / properly, the epoxy invariably will cure “tacky” or with blotches. Thorough mixing of parts A & B can be more difficult when both are of the same color, in which case hardness testing is even more important, to ensure that the product has been measured, mixed, and cured properly.
When the end user feels that the mixing & curing is in order, the epoxy should be evaluated on some mock-up substrates, which have been properly treated / prepared (if possible). This will provide added assurance that all will proceed well when the epoxy is used on the actual substrates.