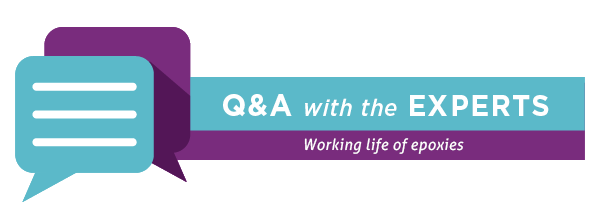
Join Venkat Nandivada, Manager of Technical Support at Master Bond, as he answers questions about the working life of epoxy adhesives.
Q: How does Master Bond define working life?
A: Different manufacturers/suppliers may use different conventions to define the working life, pot life, and gel time of an epoxy. Often, these terms are interchangeably used, and it is important to pay attention to the way each individual formulator defines these parameters.
In selecting an adhesive, sealant, coating, and potting compound, careful consideration should be given to the processing & handling requirements. One such requirement is the working life of an epoxy. After thoroughly mixing the resin and curing agent of a two component room temperature curing epoxy, its viscosity tends to increase over time. This increase in the viscosity depends on the specific compound selected, and there is a limited time frame available to properly dispense or handle the epoxy, before it gels or sets-up. This time frame is considered as the working life of the epoxy. Once the mixed epoxy gels, it can no longer be dispensed or handled.
Q: How can the working life of an epoxy be determined?
A:Although there may not be an industry wide method that provides a way to measure the exact working life of an epoxy, one indicator of the working life of an epoxy is its gel time. The gel time can be measured at room temperature, using a gel time tester. For example: if the gel time of a two component epoxy is measured to be 30 minutes at room temperature, it would mean that the viscosity of the mixed epoxy continues to increase within 30 minutes, at which point it gels. Therefore, the time frame available to properly apply or handle the epoxy (which is the working life) would be less than 30 minutes.
Q: What impact does the temperature have on the working life?
A: For two component room temperature curing epoxies, and some one component heat curing epoxies, the working life is shortened at elevated temperatures. In other words, the epoxy will gel or set-up faster at elevated temperatures, as compared to room temperature.
Conversely, when a two component room temperature curing epoxy is mixed at a lower temperature, the working life is typically longer.
Q: What are the benefits and trade-offs of short working life?
A: An epoxy with a short working life at room temperature gels or sets up quickly. Therefore, in applications where quick handling of the bonded assembly is required, an epoxy with a short working life or fast gel time can be utilized. However, these epoxies are typically more exothermic. Therefore, it may not be feasible to mix larger quantities at a time (such as pints or quarts), due to the high exotherm involved as well as fast set-up, making them not suitable for large volume potting applications. During the adhesive selection process, the tradeoffs of not having a long time to work with the mixed epoxy (before it gels) must be factored.
An example of a two component room temperature curing epoxy with a short working life or quick set-up is Master Bond EP51M. Its gel time at room temperature is around 3 to 5 minutes for 100 grams of the mixed epoxy.
Q: What are the benefits and trade-offs of long working life?
A: An epoxy with a long working life at room temperature would mean that it gels or sets-up slowly. This is particularly useful in applications where a large amount of the epoxy (such as quart or gallon) needs to be mixed at a time. Therefore, in applications where the bonding area or potting volume is relatively large, such epoxies can be utilized. These epoxies typically generate very low exotherm during the curing process.
Q: Can you give an example of a real life application, where an epoxy with long working life was used?
A: Master Bond two component epoxy EP29LP, which offers a working life of over 10 hours (for 100 grams) at room temperature, has been successfully utilized by Phoenix Scientific Inc. (PSI), as a reference surface for vehicle scanner calibration. A 15 feet long, 4 inch wide, 8 inch tall, aluminum 6061-T6 I-beam covered with EP29LP was chosen for this application. It was crucial to choose a low exotherm epoxy that could be applied in such large quantities. The application would occur in a low humidity environment over a multiple day period, and the product had to cure to a hard, smooth finish.1
Master Bond EP29LP proved to be the best reference surface when considering stability over time, and robustness. The compound also addressed the critical flatness issue. It also exhibits low viscosity and since it cures slowly, it provided a long enough working life to allow the epoxy to flow to a flat resting state without hardening prematurely. The researchers noted three characteristics of the epoxy necessary for the application: low viscosity, slow cure time, and minimally exothermic.2
This case study illustrates that faster cure is not always better, and in fact the slow curing nature of this product provided a long working life to make its application feasible in many potting/casting applications similar to this. To read the full case study please click here.
Q: Are there products which offer “unlimited” working life at room temperature?
A:We mainly looked at two component epoxy systems, but there are heat curable one component epoxy chemistries, which offer an “unlimited” working life at room temperature. These systems can be formulated to not gel or cure at room temperature, while offering a quick cure at elevated temperatures. It must be noted that although these systems provide an unlimited working life at room temperature, they do not automatically qualify as being suitable candidates for potting applications, since many such products can be exothermic in thick sections. Therefore, a range of factors need to be taken into account while selecting such compounds, and based on the handling and processing constraints, as well as the operating conditions in the final device, the epoxy choice can vary.
Reference
1, 2Reference Surfaces for Scanner Calibration, Phoenix Scientific Inc. Reference Surfaces for Scanner Calibration. January 29, 2002
Meet Our Tech Expert: Venkat Nandivada
Venkat Nandivada has been the Manager of Technical Support at Master Bond since 2010. He has a Masters in Chemical Engineering from Carnegie Mellon University. He analyzes application oriented issues and provides product solutions for companies in the aerospace, electronics, medical, optical, OEM and oil/chemical industries.
Popular epoxies with long working life
![]() |
EP29LP Clear, two component epoxy system has long pot life. Convenient one to one mix ratio. High bond strength. Superb chemical resistance properties. Used in bonding, sealing, potting and filament winding applications. Low viscosity compound. Exceptionally low exotherm. Cures rigid. Service operating temperature range from -60°F to +250°F. |
![]() |
EP21LVSP6 Two component epoxy has very low exotherm, Suitable for large casting applications. Low viscosity formulation cures at room temperature. Extended working life. Serviceable from -60°F to +250°F. Magnificent electrical insulation properties. Excellent physical strength. |
![]() |
EP62-1LPSP Low viscosity, optically clear epoxy with superior electrical insulation properties. Thermal stability. Exceptional chemical resistance. Long working life. Low exotherm. Withstands 1,000 hours 85°C/85% RH. Meets NASA low outgassing specifications. Serviceable from 4K to +400°F. |