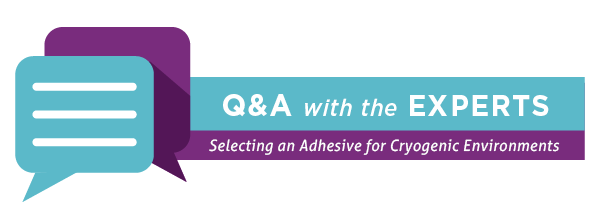
Join Jimee Patel, SDS/Safety Specialist, for a Q&A about the role cryogenic temperatures play in selecting an adhesive for low temperature applications.
Q: How do extremely low temperatures affect adhesives and the substrates they are used with?
A: The widely varying effect of cryogenic temperatures on materials complicates efforts to bond, seal, coat, or encapsulate assemblies in various applications. Withstanding cryogenic temperatures can be challenging for many substrates, and this extreme exposure can also cause some adhesives to become brittle and fracture or lose adhesion.
Most silicone adhesives are able to retain their performance down to about -60°C, and some specialized silicones can perform well down to -100°C to -120°C. On the other hand, specialty epoxy formulations have been designed specifically for maintaining performance and delivering the required physical, thermal, and electrical characteristics at liquid nitrogen (77 Kelvin or -196°C) or as low as liquid helium temperature (4 Kelvin or -269°C).
Q: What are some of the factors an engineer should consider when selecting an adhesive for applications exposed to cryogenic temperatures?
A: Adhesive selection depends on many factors such as the operating temperature range, the thermal cycle ramp speeds and dwell times at the extremes, the substrates as well as their configuration, the coefficient of thermal expansion (CTE) mismatches between the substrates, the electrical properties needed (such as electrical insulation or electrical conductivity), the thermal properties needed (such as thermal conductivity), chemical resistance requirement, and the outgassing constraints. Other factors that engineers should consider include the handling and processing requirements such as cure time, cure temperature restrictions, and the automation capabilities. While selecting the right adhesive, all of the benefits conferred must be balanced with the tradeoffs of each system selected.
Q: What products does Master Bond formulate to match the extremities from a cryogenic standpoint?
A: Master Bond offers several epoxy systems, which are well-suited for cryogenic applications. Some of these epoxies also offer excellent resistance to high temperatures (as high as 200 °C). A few examples would be:
EP29LPSP: Serviceable from 4K to 125°C. Two part, low viscosity epoxy system is optically clear, and NASA low outgassing approved.
EP21TCHT-1: Serviceable from 4K to 200°C. Two part epoxy with paste consistency is easy to apply and withstands 1000 hours at 85°C /85% RH.
SUP10AOHT-LO: Serviceable from 4K to 200°C. One part epoxy has excellent thermal conductivity and superior electrical insulation.
EP21TDC-2LO: Serviceable from 4K to 125°C. Two component, highly flexible epoxy resin compound used for high performance bonding, sealing, coating, and encapsulation.
Q: What role does glass transition temperature (Tg) play in applications involving cold temperature extremes?
A: In cold temperature applications, the Tg does not provide the same clear window into adhesive performance as it does in high temperature applications, unless one is considering using a silicone. The dip in temperatures much below the Tg, in general, causes all adhesives no matter the make up to become stiffer, and in many cases more brittle. Theoretically, that reasoning would seem to favor flexible adhesives with low Tg for the coldest applications. However, for many silicones, the drastic difference in the stiffness below the Tg (as compared to above the Tg) renders them not usable for extreme cryogenic environments.
From a practical standpoint, the opposite is often true. Many epoxy adhesives which are rigid at room temperature, do not experience a considerable loss of properties even at cryogenic temperatures, implying they work best in a rigid state that extends from their Tg into far colder territory. Master Bond offers certain one and two component epoxy adhesives that provide structural bonds, serviceable from a cryogenic 4 Kelvin to as high as 200°C.
Q: Which adhesives are chosen for use in severe environments that mix extreme cold and heat?
A: Typically, epoxies are the preferred choice in such situations. They have a proven track record in applications involving exposure to extreme cold, heat, and aggressive thermal cycling. They can actually be formulated with enough toughness to withstand extreme temperature fluctuations. These epoxies are typically toughened through the addition of a rubber or elastomeric modifiers that makes the adhesive less stiff and not as susceptible to cracking, as compared to other systems. New epoxy formulations have been developed that provide a high Tg while still preserving the toughness needed to withstand extreme environments as well as thermal cycling stresses.
Silicones are another adhesive family well suited to certain thermal cycling applications due to their outstanding flexibility and elasticity. Some silicones are capable of withstanding temperatures as low as -115 C, and as high as 250 C. Silicones rarely crack under thermal cycling because they inherently offer a winning combination of high-temperature resistance and flexibility as long as they are operating above the Tg, and below their maximum service limits. These properties make silicones the best material for resisting thermal shocks or rapid temperature changes. The main downside to silicones is that they are not structural, and are more limited in their lower temperature limit as compared to many epoxies.
Q: What should one be mindful of regarding the curing process for such adhesives?
A: Specific grades of adhesives can be cured at room temperature or at elevated temperatures, for faster cures. To optimize the properties of an adhesive which is capable of curing at room temperature, it is often recommended to cure overnight at room temperature, followed by a post cure with heat for a certain number of hours. It is suggested to check with the manufacturer of the adhesive, for the appropriate cure schedule recommendation, based on the overall application requirements as well as processing constraints.
Adhesives for Cryogenic Temperatures
![]() |
Two component, low viscosity, modified heat cured epoxy system for bonding, sealing and coating. Formulated for service at cryogenic temperatures and capable of withstanding cryogenic shock. Meets NASA low outgassing requirements. Optically clear. |
![]() |
EP21TCHT-1 Two part, room temperature curable epoxy system with high thermal conductivity. Serviceable from cryogenic temperatures up to +400°F. Electrically isolating. Meets NASA low outgassing specifications. Halogen free. Paste consistency. Formulated to cure at ambient temperatures. Withstands 1,000 hours 85°C/85% RH. |
![]() |
Supreme 10AOHT-LO Thermally conductive and electrically insulative, one part epoxy adhesive. Superior toughness and dimensional stability. Bonds are resistant to thermal cycling and many chemicals. Serviceable from 4K to +400°F. NASA low outgassing approved. Withstands 1,000 hours 85°C/85% RH. Impressive physical strength properties. |
![]() |
EP21TDC-2LO Highly flexibilized, thermally conductive/electrically insulative epoxy adhesive. High elongation. Exhibits superior shear and peel strength properties. Serviceable from 4K to 250°F. Withstands thermal cycling, thermal shock and mechanical shock. Passes NASA low outgassing test. Cures at room temperature or more quickly at elevated temperatures. |